Discover the key differences between hydraulic block machines and traditional block-making methods. Learn how each impacts efficiency, cost, quality, and sustainability in construction projects.
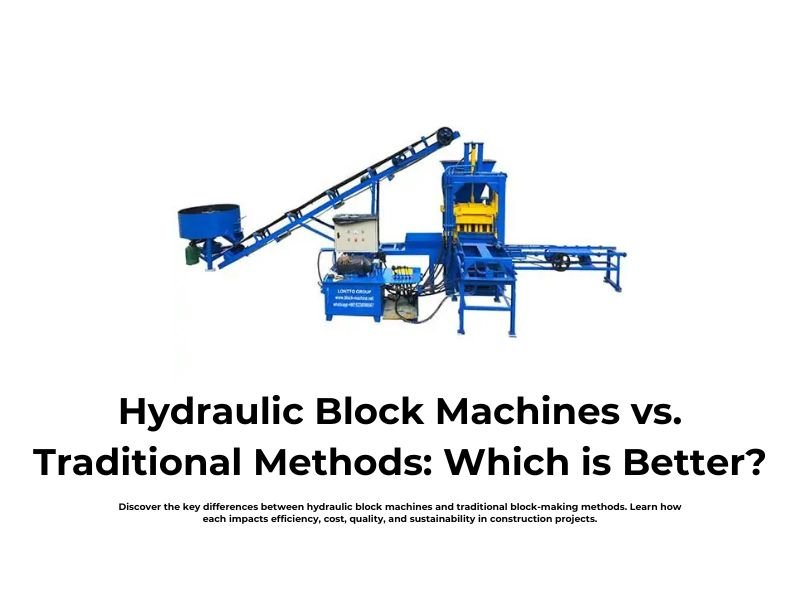
In the construction industry, block-making is a cornerstone of creating durable structures. Over the years, the process has evolved, with hydraulic block machines becoming a prominent alternative to traditional methods. These machines promise increased efficiency, consistent quality, and cost-effectiveness. But how do they stack up against the tried-and-tested manual methods? In this comprehensive guide, we’ll delve into the strengths and weaknesses of both, helping you choose the right approach for your construction needs.
1. Efficiency
Hydraulic Block Machines:
- Equipped with automated systems, these machines produce blocks faster and more consistently.
- Capable of manufacturing hundreds of blocks per hour, reducing project timelines significantly.
- Require minimal manual intervention, making them ideal for large-scale projects.
Traditional Methods:
- Labor-intensive and time-consuming, producing fewer blocks per day.
- Heavily reliant on skilled labor, leading to potential delays if workers are unavailable.
- Best suited for smaller projects where speed is not a priority.
2. Cost Implications
Hydraulic Block Machines:
- Higher initial investment due to advanced machinery and technology.
- Long-term savings from reduced labor costs and lower material waste.
- Energy-efficient models contribute to operational cost reductions over time.
Traditional Methods:
- Low initial costs as they rely on simple tools and manual labor.
- Higher long-term expenses due to inefficiencies and inconsistent block quality.
- Increased material waste can inflate overall project costs.
3. Quality and Consistency
Hydraulic Block Machines:
- Produce uniform blocks with precise dimensions, ensuring structural integrity.
- Advanced pressure systems enhance the density and durability of blocks.
- Ideal for projects that require strict quality control standards.
Traditional Methods:
- Prone to inconsistencies in block size and shape, affecting construction stability.
- Quality depends heavily on the skill and expertise of the workers.
- May result in uneven surfaces, leading to additional finishing work.
4. Environmental Impact
Hydraulic Block Machines:
- Eco-friendly options are available, reducing carbon emissions.
- Minimized material waste contributes to sustainable practices.
- Compatible with alternative materials like fly ash and recycled aggregates.
Traditional Methods:
- Generate more waste due to inefficiencies in the manual mixing and molding process.
- Often rely on resource-intensive techniques, increasing environmental degradation.
- Limited compatibility with eco-friendly materials.
5. Labor Requirements
Hydraulic Block Machines:
- Require fewer workers as most processes are automated.
- Easier to train operators, reducing dependency on skilled labor.
- Improved workplace safety with minimal manual handling of heavy materials.
Traditional Methods:
- Labor-intensive, requiring a large workforce to maintain output.
- Higher risk of workplace injuries due to manual handling and repetitive tasks.
- Relies heavily on experienced workers, making it challenging to scale operations.
6. Versatility
Hydraulic Block Machines:
- Capable of producing a wide range of block types, sizes, and shapes.
- Easily adjustable to meet specific project requirements.
- Suitable for applications such as pavers, hollow blocks, and solid blocks.
Traditional Methods:
- Limited to basic block designs and sizes.
- Lack of flexibility can be a disadvantage in projects with diverse requirements.
- Customization often requires additional labor and tools.
7. Maintenance and Longevity
Hydraulic Block Machines:
- Durable and designed for long-term use with proper maintenance.
- Regular upkeep ensures consistent performance and reduces downtime.
- Manufacturers often provide after-sales support and spare parts.
Traditional Methods:
- Simple tools require minimal maintenance but wear out quickly.
- Frequent replacements and repairs can disrupt workflows.
- Not designed for long-term, high-volume production.
Use Cases of Hydraulic Block Machines
- Large-Scale Construction Projects: Efficiently meet high demands for blocks in urban and industrial developments.
- Eco-Friendly Projects: Leverage alternative materials for sustainable building practices.
- Custom Design Needs: Produce blocks tailored to specific architectural and structural requirements.
Conclusion
When comparing hydraulic block machines and traditional methods, the choice largely depends on your project’s scale, budget, and quality requirements. Hydraulic block machines clearly stand out for their speed, efficiency, and sustainability, making them a preferred choice for large-scale and modern construction projects. However, for smaller-scale or cost-constrained projects, traditional methods may still be viable.
Investing in hydraulic block machines can lead to long-term savings, enhanced block quality, and a reduced environmental footprint, setting a strong foundation for sustainable construction practices.