Discover the benefits of concrete mixers with automatic loading systems, their efficiency in construction, cost savings, and technological advancements in modern concrete mixing.
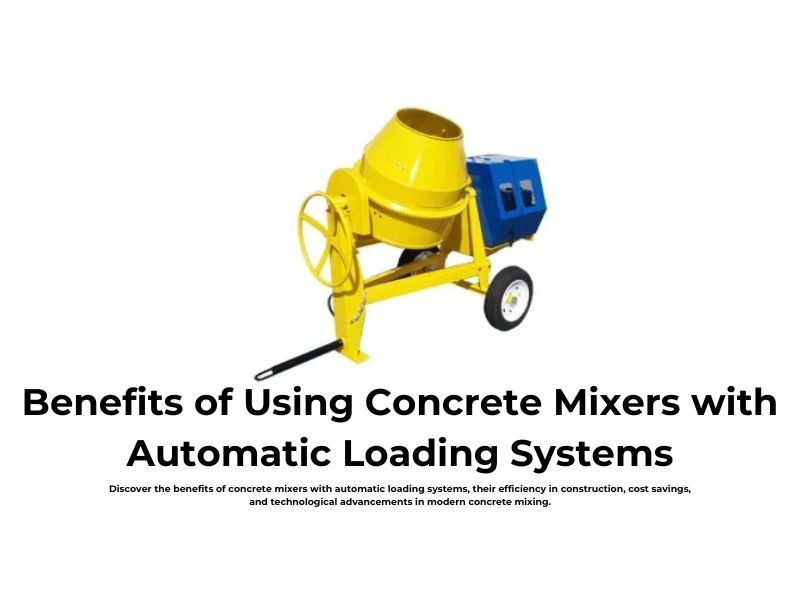
Concrete mixers with automatic loading systems have revolutionized the construction industry, bringing a new level of efficiency, cost-effectiveness, and operational simplicity. This article explores their benefits, applications, and the technological advancements that make them indispensable tools for modern construction projects.
1. Introduction to Automatic Loading Concrete Mixers
Concrete mixers with automatic loading systems are specialized machines designed to streamline the process of mixing and transporting concrete. Unlike traditional mixers that require significant manual input, these machines are equipped with systems that automate the loading, mixing, and discharging processes.
How Do They Work?
- Automatic Loading: Equipped with a self-loading bucket, the machine scoops the required raw materials (cement, sand, aggregate, and water) automatically.
- Mixing: A rotating drum ensures homogeneous mixing of concrete.
- Transport and Discharge: The mixed concrete is transported to the site and unloaded with precision.
Key Components of Automatic Loading Concrete Mixers
- Self-Loading Bucket – Automates material feeding.
- Rotating Mixing Drum – Ensures even and consistent concrete mixing.
- Hydraulic Systems – Facilitates lifting, loading, and discharge.
- Cabin Controls – User-friendly interface for the operator.
2. Top Benefits of Concrete Mixers with Automatic Loading Systems
2.1 Increased Efficiency and Productivity
The self-loading feature reduces manual labor, leading to faster operations. The machine completes the tasks of loading, mixing, and transporting within a single cycle.
- Efficiency Improvement: Reduces operational delays and streamlines the workflow.
- Higher Output: Suitable for large-scale projects requiring continuous concrete supply.
Example: A self-loading mixer can produce up to 4 cubic meters of concrete per batch, saving hours of manual labor.
2.2 Cost Savings
Automatic loading systems significantly reduce costs associated with:
- Labor: Fewer workers are needed to load and monitor the mixer.
- Material Wastage: Precise loading ensures minimal raw material loss.
- Time Savings: Faster operations translate to reduced project duration, saving costs.
Compared to traditional mixers, project costs can decrease by 15-20% due to automation.
2.3 Versatility and Flexibility
Automatic loading mixers are versatile, suitable for various construction environments, including:
- Urban Infrastructure
- Road Construction
- Residential Buildings
- Remote Construction Sites
Their compact size and maneuverability allow them to operate in tight spaces and challenging terrains.
2.4 Precision in Mixing and Material Proportioning
Automated systems allow precise control over:
- Material Quantities: Pre-measured ingredients for consistent quality.
- Mixing Time: Optimal mixing duration to ensure homogeneity.
This ensures high-quality concrete that meets project specifications.
2.5 Enhanced Mobility and On-Site Flexibility
Unlike stationary batching plants, automatic loading mixers can move across sites, ensuring:
- Concrete is Delivered On-Demand: Fresh concrete delivered directly where needed.
- Eliminates Delays: No dependency on external transportation.
Mobile mixers are ideal for remote and off-grid construction projects.
2.6 Reduced Environmental Impact
By automating the process, self-loading mixers reduce waste and energy consumption, supporting sustainable construction. Key environmental benefits include:
- Less Wastage: Precise material proportioning reduces excess usage.
- Fuel Efficiency: Modern machines are designed to consume less fuel per cycle.
3. Applications of Automatic Loading Concrete Mixers
3.1 Urban Construction
From building foundations to paving roads, automatic loading mixers deliver efficiency in urban construction projects.
3.2 Remote and Rural Projects
Self-loading mixers are invaluable for rural development, where access to stationary batching plants is limited.
3.3 Infrastructure Development
Ideal for large-scale infrastructure projects such as bridges, tunnels, and highways.
4. Technological Advancements in Automatic Loading Concrete Mixers
4.1 GPS-Enabled Operation
Modern mixers are equipped with GPS tracking for real-time location monitoring and productivity tracking.
4.2 Digital Control Panels
User-friendly interfaces allow operators to set parameters for loading, mixing, and discharging with accuracy.
4.3 Fuel-Efficient Engines
Advanced engines reduce emissions and fuel consumption, aligning with green construction practices.
5. Comparison: Automatic Loading Mixers vs Traditional Mixers
Features | Automatic Loading Mixers | Traditional Mixers |
---|---|---|
Labor Requirement | Minimal (Automated) | High (Manual Loading) |
Efficiency | High | Moderate |
Precision | Accurate Material Proportioning | Manual Estimations |
Cost-Effectiveness | Reduced Overall Costs | Higher Labor and Time Costs |
Portability | Mobile and Versatile | Limited Mobility |
6. Future Scope of Automatic Loading Concrete Mixers
The demand for automatic loading concrete mixers is expected to grow due to:
- Increased Infrastructure Development: Rapid urbanization and smart city projects.
- Technological Integration: IoT-enabled mixers for real-time monitoring and efficiency optimization.
- Green Construction Initiatives: Machines designed with eco-friendly fuel systems and emission controls.
Market Growth
According to industry reports, the global market for self-loading concrete mixers is projected to grow at a CAGR of 7-8% over the next five years.
7. Conclusion
Concrete mixers with automatic loading systems are transforming the construction industry with their unmatched efficiency, cost-effectiveness, and technological advancements. They not only streamline operations but also ensure high-quality concrete production, making them an essential tool for modern construction projects.